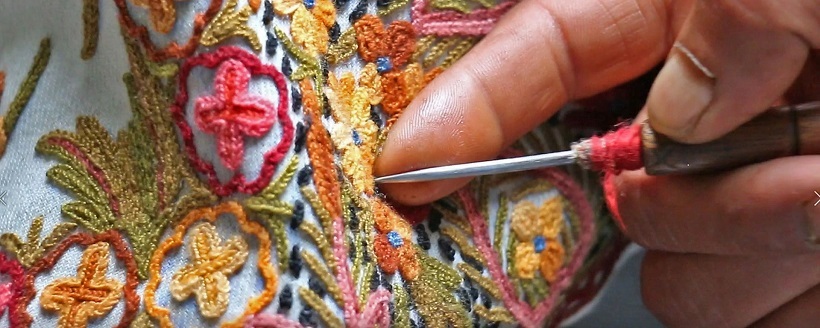
An artisan’s anguish apart, the current situation is only creating existential crisis for Kashmir’s golden hands amid the growing dominance of machines in the handicraft sector.
WHEN Shameem Magray was young he happily chose workshop over school.
He along with his bunch of friends learned embroidery at his neighbor’s house. Since then Magray has been working in this field and is a master of all hand-made embroidery techniques.
“You tell me what you want and I will make it,” says the confident artisan who has been in the field for 35 years. “It may take some time but the product will be everlasting.”
But while he put in a lot of hard work in the work, he only earns about Rs. 500 per day for his 12-hour work.
Kashmir’s embroidery popularly known as Kashida embroidery is one of the most popular needleworks from the subcontinent.
Be it Pashmina shawls with exotic Sozni embroidery designs, or the crewel embroidered curtain in Kashmiri houseboats, or the embroidered rugs or the chain stitch cushions, all these embroideries techniques have been followed by Kashmiri people for a long time.
For summers, the base material used for Kashida is light-colored wool or cotton cloth. It’s a thick-black wool cloth for winters.
Birds, animals, trees, leaves, and many other motifs are embroidered with colorful threads and beads on the cloth by artisans.
Kashmir was ruled by different regimes for centuries, whose influence can be seen on Kashmiri textiles.
During 1420-70 AD, a paper by Deborah Emmet notes, Zain-Ul-Abidin, the eighth sultan of Kashmir, brought shawl and carpet weavers to the valley from Turkestan and Samarkand respectively. It is believed that crewel and chain stitch embroidery was introduced in the valley during his reign.
The world-famous Kashmiri Pashmina shawl industry came into existence in the late sixteenth-century under the rule of Mirza Haider Dughlat, claims the paper.
“A patron of the arts of Kashmir,” the paper mentions, “he [Dughlat] is said to have introduced the concept of using pashm from Ladakh to be woven into shawls by the expert craftsmen of Kashmir who had previously used sheep’s wool.”
Zamir Naqash, the owner of Naqash Design, deals with Sozni and crewel embroidery techniques for a long time. His father started the manufacturing of Kashmir textiles with different embroidery techniques. When he joined the business, he started exporting the textiles.
“The integrity of handmade products is very different,” admits Naqash who only works in handmade embroidery. He claims that they try to create products that are better than machine-made products and stand out in the market.
Sozni embroidery is considered to be done by the most skilled embroiderers in the valley. Earlier it was a man-dominated field but with time many women have also joined the workforce.
This embroidery technique employs a needle in which identical motifs are created on both sides of the fabric. Sometimes different colors are used for the same motif on the two sides. Two or three artisans work on one shawl and it takes any time between one month and a year to complete depending upon the design.
Since the fiber used to weave Pashmina shawls are made of a fine variant of the animal hair fiber, only fine Sozni embroidery is suitable for them.
The artisans make a stencil of the design on the cloth using “engraved wooden blocks dipped in a watery solution of charcoal powder mixed with a type of binder”.
Woodworkers called ‘Naquash Gurs’ engrave the wood blocks with fine details. Many Sozni artisans are dependent on these blocks because of their fineness and long-lasting impressions.
Once the pattern and colors are decided, each fabric is given to a craftsman because each handwork is distinct. Mostly used motifs are abstract geometric designs, multi-colored flowers, and paisley patterns.
Batin Iqbal, who runs Batin Textiles and Handicrafts, has been working on Aari embroidery techniques for a long time.
In this embroidery, a thread of varying thickness and fineness is used and stitched with the help of a hook called Aari, explains Iqbal.
The thread used for the embroidery is selected according to the Aari and fineness of the stitches. Each craftsman makes his hook with a steel needle that is attached to a wood handle.
The hook is always under the fabric on which embroidery is done. It moves along the design pattern. The stitch is done from one point. And to create an emboss effect on the fabric the stitch rotates around the point.
Crewel designs are larger than other embroideries and the most common patterns are flowers, birds, and paisley. Each flower is given a name by the craftsman, says Iqbal
The crewel work is done mainly on drapes, cushion covers, bedspreads, shopping bags, upholsteries, and handwoven Dasooti (double twist) cloth by the hook.
Two types of crochet hooks – smaller hook and larger hook are used for this embroidery. For fine quality crewel and chain stitch work, smaller hooks are used whereas for quick work, larger hooks are used.
Emmet mentions in her paper that although the crewel embroidery field was dominated by men but currently many women have started working in chain stitch and crewel embroidery as men prefer to get jobs that pay them higher.
“Very few embroiderers are now prepared to do the very fine hook work. It takes a long time to complete limited meterage,” notes the paper.
But at the same time, says Iqbal, the supremacy of machines is also discouraging many artisans to switch over to other means of living.
“Although most of the Aari work is now carried out by machines,” he says, “the finish and quality is better in handmade products.”
But, the entrepreneur says, as the demand for production increased, manual and computerized machines have been employed by manufacturers.
“In computerized machines,” Iqbal says, “one-man can-do work of 20 men.”
Owing to the condition in the valley and the evolution of machine-made embroidery, many artisans working in this field are suffering a lot.
When Ajaz Tramboo was 22 years old, he wanted to find a job but his father insisted that he should join their old family business of embroidery work. As a fresh graduate, Tramboo found the work quite interesting and started expanding the business.
“We had many showrooms in Kashmir and outside the valley,” says Tramboo. But with machine-made embroidery coming to the market, the handmade embroidery business started facing a crisis, laments the 50-year-old businessman.
Tramboo admits that he also started machine-made embroidery work but he was not satisfied.
“I thought I was going away from the rich Kashmiri culture in which my father has spent so much time,” he says. “So I decided to stick to hand-made embroidery.”
He says apart from the machine-based embroidery, the turmoil in the valley has affected the business badly. At times, he says, he’s not able to send materials to his customers on time due to which they are not satisfied with his service and shows a lack of interest.
“We had three stores in Srinagar but as the conditions in the valley deteriorated our stores were shut down,” Tramboo says.
According to Aaditya Kitroo, co-founder of Jos&fine, when machine-made products came in the market, the hand-made products started showing a decline.
In the machine, he explains, the Aari needle fires at a very high speed so the fabric has to be moved quickly and the end-product does not have clean lines unlike in handmade embroidery.
Kitroo recalls a conversation he had with some elder artisans who told him that in the 1990s, each day three trucks full of fabric used to go from Srinagar to Anantnag for embroidery and 1000 people used to work on these fabrics.
“If I compare the condition of handmade embroidery products in the early 90s,” Kitroo says, “it is less than 20% of what it was at that time.”
Though many artisans are continuing the legacy which their forefathers have started but they are quite uncertain about the future of the legacy.
Naqash feels that after 30 years Kashmir may lose hand-made embroidery technique. He thinks that the new generation of Kashmir has less respect for the embroidery business and they are not interested in carrying it forward. He hopes that with time Kashmiris may realize that they had “something special” which should be treasured.
Unquestionably problems exist for handmade embroidery artisans in the valley but the upcoming younger generation is also working to revive the cultural heritage.
Many young people are seen wearing designer pherans with intricate embroideries and they take pride in wearing the traditional local dress. Young entrepreneurs like Iqra Ahmad are working on the traditional tilla embroidery technique.
Gold and silver tilla threads are used for this kind of embroidery. It is a traditional Kashmiri craft used in pherans, salwar kameez, and other garments. Chinar, lotus, almond are some of the common motifs designed by tilla embroiderers.
No matter what is the financial condition of the family, each bride is supposed to have a tilla pheran or a tilla shawl in her wardrobe.
According to historians, tilla embroidery originated from a remote village of Zari in Iran and it entered Kashmir when Muslim saint-reformer Mir Sayeed Ali Hamadani came to Kashmir along with his associates, the majority of whom were craftsmen. The reformer is being credited for empowering Kashmiris through skill development and created what many call the tribe of “golden hands” in the valley.
Despite many people preferring machine-made embroidery over handmade embroidery, Kitroo believes that due to coronavirus the market has shifted towards conscious consumption and people are looking at handmade products a bit more.
However, people may not buy products like pashmina which are costly but economical handmade products like cushion covers, handmade rugs, and bedsheets will be on their list.
Follow this link to join our WhatsApp group: Join Now
Be Part of Quality Journalism |
Quality journalism takes a lot of time, money and hard work to produce and despite all the hardships we still do it. Our reporters and editors are working overtime in Kashmir and beyond to cover what you care about, break big stories, and expose injustices that can change lives. Today more people are reading Kashmir Observer than ever, but only a handful are paying while advertising revenues are falling fast. |
ACT NOW |
MONTHLY | Rs 100 | |
YEARLY | Rs 1000 | |
LIFETIME | Rs 10000 | |